Plunger type Screen Changer
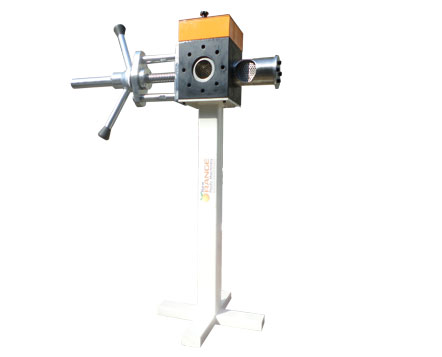
Technical Specification
*Design and Technical Specification should change prior to information
Sr No. | Model | Power in K.W. | Filter size in MM |
---|---|---|---|
1. | NOPM-60 | 1.2 K.W. | Dia.60 |
2. | NOPM-80 | 1.6 K.W. | Dia.80 |
3. | NOPM-90 | 2.4 K.W | Dia.90 |
4. | NOPM-100 | 3.2 K.W. | Dia.100 |
Operation:
Stop the Plant and change the filter station with the help of Puller Handle OR Cylinder. Now, start the Plant. Remove the old chocked mesh and put new mesh is in it while running the Plant.
Application:
- Pipe Plant
- Mono Layer Plant
- Multi Layer Plant
- Lamination Plant
- Co-extrusion Plant
- PVC Recycling Plant (Special Design)
- Sheet Plant
- Sutli plant
- Mono Filament Plant
- Profile Plant
- Pen & Tubing Plant
Advantages:
- Filter remove the impurities and prevent the damages of Die.
- Filter improves the quality of final product.
- If it is Hydraulic operated so plant output will we increased compare to manual operating.
- Eliminate the idle time and easy to operate.
- Easy maintenance.
- Wear resistance proof.
Optional Availability:
- Barrel & Die side fitting arrangement along with heaters and fasteners.
- Extra Heaters.
- Extra filters & Breaker Plates.
- Special design for PVC and Engineering Plastic Plant on extra cost.
- Accumulator system will provide if required.
- Heating Panel will provide for Screen changer heating.
- Pressure Transducer system will provide for improves life of Extruder and screen changer.
- Special timing panel and extra arrangement also provide to avoid accident.
- Fabricated / Wheel mounted stand for support / movement of Screen Changer.